9:11 am
Starting an Oil Change Business? Ensure a Smooth Engineering and Design Process

If you are opening a franchise location for a quick lube or automotive service and repair business, your corporate franchise will provide you with their facility design plans (called the ‘design standard’). Often, it will be up to you to hire an engineering firm to customize these plans to meet the municipal permitting requirements for your location. When starting an oil change business, start off on the right foot. Here are a few things you need to know before you look for an engineering and design partner.
Why do I need an engineering/design firm?
Because each municipality has its own unique bylaws, processes, and procedures around development – and no two sites are ever the same – the corporate design standard is not a one-size-fits all solution.
Whether you’re building a brand new (greenfield) facility or moving into an existing building, you will require the services of a qualified engineering and design firm. Their job is to work with you (and your franchise head office) to successfully guide your project through the municipal permitting and approvals process. The engineering firm is there to address site layout and design, building layout, structural, electrical, and mechanical design. They will also provide final inspection and sign-off on construction, to ensure it meets the approved design.
It’s important to choose an engineering design firm that has built projects in your city and is familiar with the local permitting and approval process. Make sure they have expertise in the automotive service sector. You’ll make your life way easier by hiring a firm with full-service engineering (civil, structural, mechanical, and electrical), project management, and architectural services all under one roof.
What does the engineering and design work encompass?
Site planning:
The design firm will be responsible for providing a wide range of civil engineering services. This includes grading, drainage, vehicular access, queuing, parking, utility hookup, etc. Another significant component of site planning is zoning bylaw compliance. Ultimately, it most often dictates the layout of the site.
Building structure:
When a new structure is to be built, it will require the involvement of a structural engineer. Their job is to ensure the building is engineered for structural stability and integrity and meets all building codes. Key considerations include foundations that suit the local soil conditions and are able to stand up to anticipated environmental loads (such as heavy spring snowfalls).
Elevations and signage:
This includes ensuring the building exterior conforms to all municipal and building code requirements from a structural and visual aesthetic perspective.
Signage is crucial to attracting customers and marketing your brand. An engineering and design firm can provide expertise and assistance to make sure you get it right. This includes recommendations on signage type and placement, and the necessary support to secure the required permits.
Because your development can have an impact on those in the community, the approval process may require varying degrees of public consultation and engagement, which can be managed by the engineering and design firm. Public feedback could dictate design changes to the landscaping, signage, and exterior building design.
Mechanical and electrical engineering:
The engineering firm will typically develop and submit plans outlining internal layout, as well as all electrical and mechanical systems (plumbing, HVAC, power service, etc.). This work will strictly adhere to all building code, Canadian electrical code ASHRAE requirements, and permitting requirements.
What special considerations are involved when engineering an oil change shop?
The design of automotive service facilities must check all of the boxes around codes, community building standards, public, and employee safety. Oil change, lubrication, and mechanical repair facilities have a few unique design requirements: from bay doors to pits to oil storage & waste systems to hydraulic hoists. The handling and disposal of fluids require extra attention: such as proper above-grade ventilation for waste oil reservoirs designed to accommodate additional stresses during the product removal process. Tanks can be located inside the facility (typically in the basement). In some cases, they may be placed above-ground for added safety. Overflow monitoring systems will need to be incorporated into the design and equipment specifications.
If lifts are used, the engineering team will need to ensure the foundation and floor structure meets load requirements. Other supporting infrastructure, such as power, may need to be upgraded to accommodate electrical loads. While older, in-ground lifts required additional protection against contamination, newer lifts are above ground and do not require the same risk mitigation.
Put your project in the fast lane
When it comes to construction, the engineering and design phase represents up to 75% of the project schedule, but only about 3 to 5% of the project budget. Given the amount of time required to obtain permits, it is well worth choosing an experienced engineering partner that can help you avoid oversights and minimize delays. Cutting corners by choosing a less experienced team can be costly. Hiring the right firm is money well spent.
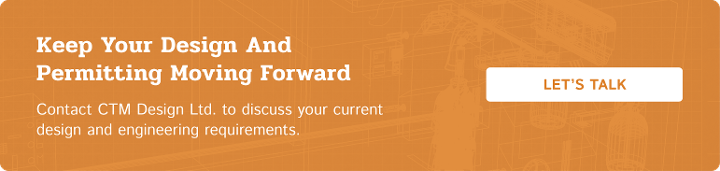